Machine vision systems in production processes
Machine vision systems, or image processing systems, are computerized systems for the automated optical inspection and control of products or production processes. Data from 2D/3D sensors and cameras are automatically evaluated in order to detect defects, secure assembly processes and guide robots when parts are being removed or loaded.
Vision systems are used for:
- DMC reading, grading, verification
- plain text recognition
- completeness checks
- optical error detection, e.g. surface testing or position detection
- optical measurement and sorting tasks
- assembly progress checks
- robot guidance, e.g. pick and place, bin picking.
To use a vision system effectively, the components must be adjusted to match the requirements and environmental conditions, as well as the production process. Alongside component selection, the individual programming of the system also plays an important role.
Data analysis in real time
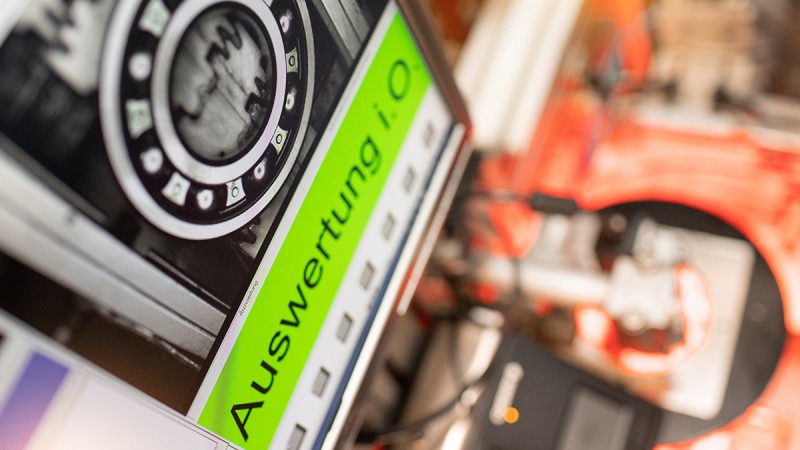
Modern image processing systems use high-resolution 2D cameras or 3D sensors, which record images of products or production processes and forward them to analysis units. There, the images can be analyzed in real time using proven and innovative algorithms. Using the digital data generated, it is possible to control and optimize processes in the production cycle. Any areas of potential in the production and testing process can be identified and optimized in a targeted manner. The result can be measured in a reduced scrap rate and thus has a positive impact on production costs.
Our vision system experts have expertise in 2D, 2.5D and 3D methods. We implement complex image processing applications for high-speed production lines. The extensive know-how of our specialists in the fields of vision sensors, embedded systems, performance and topography forms the basis for innovative and robust solutions.
Machine vision systems with artificial intelligence
Artificial intelligence is a field of expertise whose full potential is far from realized. Using machine learning methods, it allows us to perform sophisticated surface tests that cannot be captured by descriptions of error characteristics in rule-based inspection programs. Our experts train neural networks using machine learning algorithms in order to identify patterns and anomalies. To this end, various data are captured, compiled and interpreted.
We also expect artificial intelligence or subareas of that field to be used in other areas of production. At present, we are already in a position to make predictions with regard to scrap rates based on the data analyzed. In the near future, production staff will be actively encouraged to use our standby mode (eco mode). This means that, based on machine data, a suggestion to switch to standby mode is displayed on our machine displays, which can be identified from an intelligent analysis of historical values.
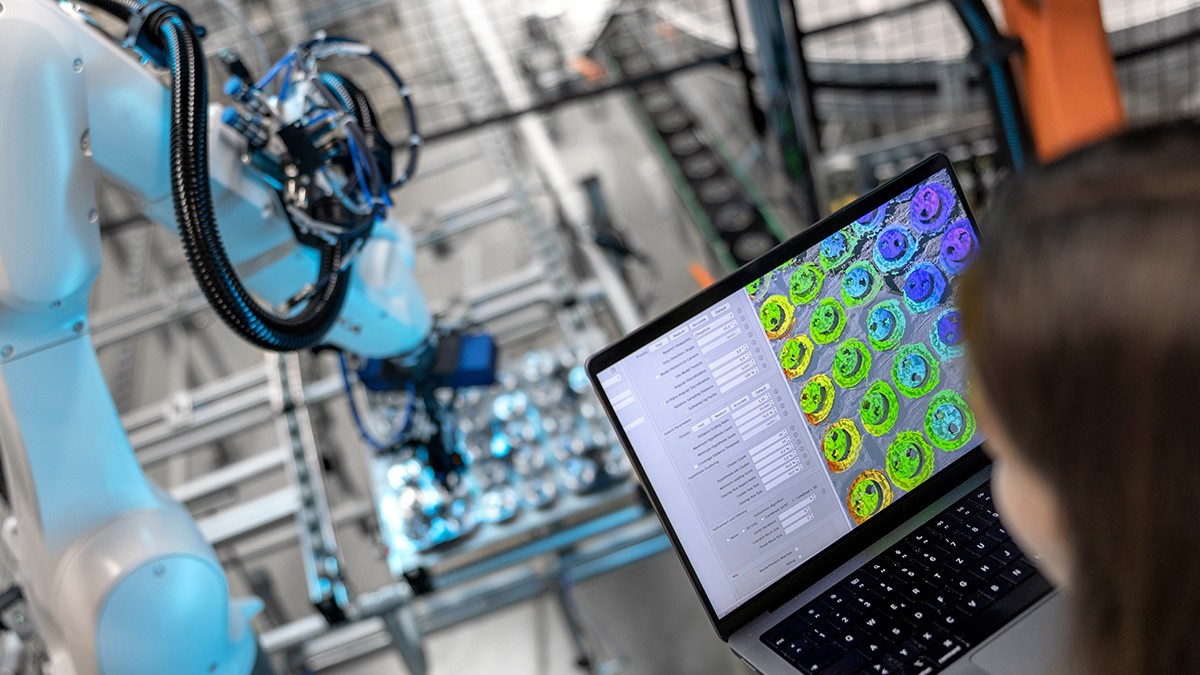
Our vision for AI-supported production
Self-learning robotic systems: These systems independently detect the components to be gripped and use the available data to define an optimum gripping position. There is no need for a human to intervene or for the system to be reprogrammed.
Machine data analyses: Historical production data are analyzed and control and maintenance recommendations made, thus making it possible for maintenance requirements to be detected early, for example.
Application highlight for vision systems
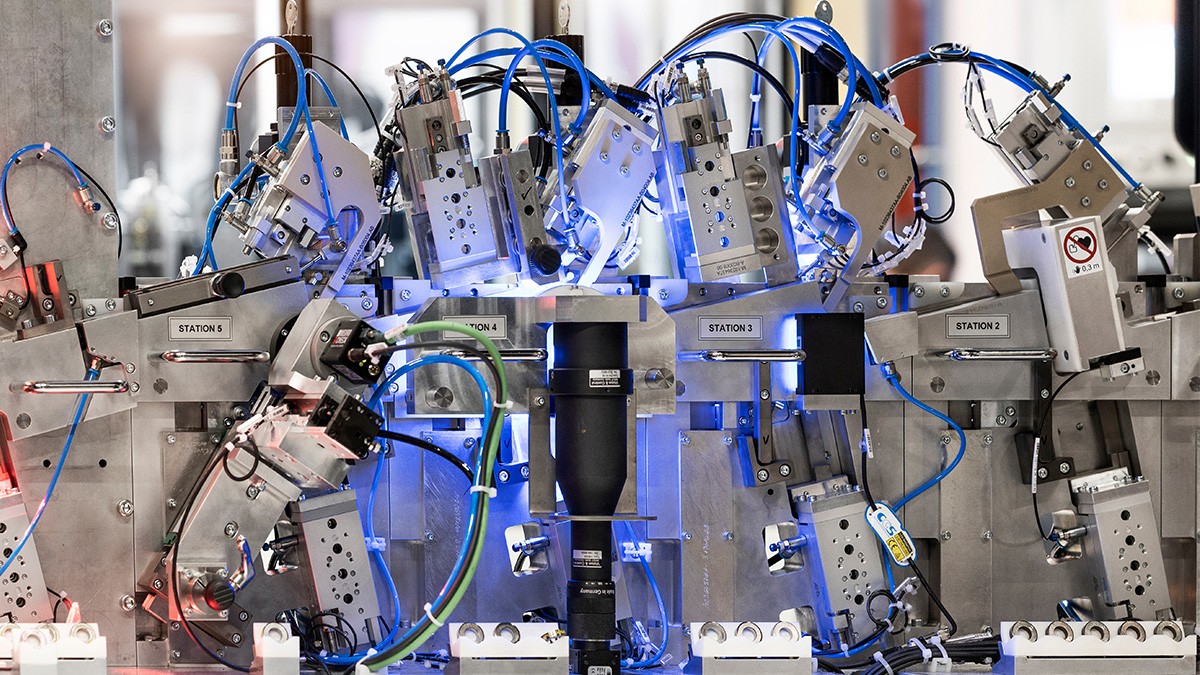
Cam rollers are bearing elements for rocker arms for valve control in internal combustion engines. Alongside measuring the inner diameter and outer width and structural testing, vision systems are also used to test cam rollers. The two end faces on the right and left, the lateral surface and the inside right and left of the bore are tested at four stations.
Thanks to our space-saving machine design, these tests – nine in total – can be carried out in an area of less than 3.5 m2untergebracht. Machine setup involves no tools whatsoever, as production parts are inserted to adjust the width and height. By additionally implementing an automated emptying function, the setup time for new types is just six minutes.
Our proprietary software for the human-machine interface allows access to the machine and to the central control system for various camera systems, including from different manufacturers. Operation can be centralized via a uniform, intuitive and simple user interface.