Customer-specific testing machines, testing systems or measurement stations
Measurement and testing technology is a broad field with many different technologies and areas of application. These processes are used in production to ensure product quality and function, for example.
Measurement and testing systems are often referred to in general terms in this context, but the objectives for determining product data are different. While a measurement results in a quantitative determination of physical variables using a measuring process, testing determines whether a test object meets specific requirements.
Our global networks of experts have extensive know-how of measurement technology and high-level expertise. They are working to continually develop and optimize the methods and systems used in our machines and systems. Working in collaboration with specialist partners, for example for camera technology or measuring sensors, we identify the best solutions for specific testing sequences.
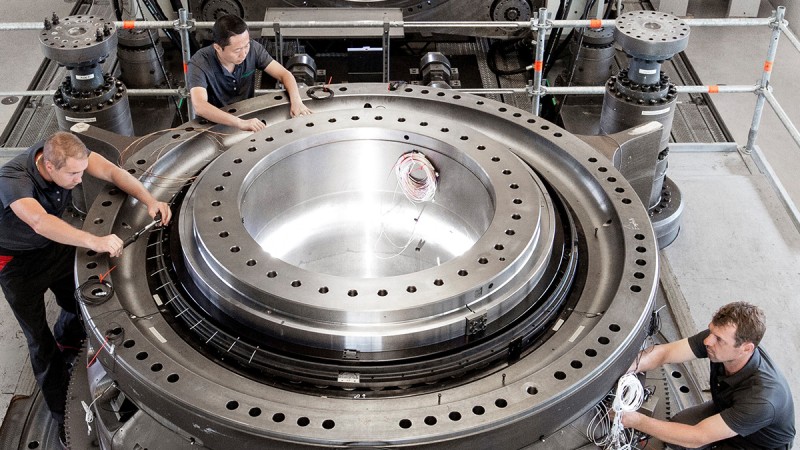
Technologies used in our measurement and testing systems
We flexibly combine different technologies from our portfolio for the components/assemblies or final products. The measurements can be carried out in manual systems or fully automatically on machines.
Single- or multi-dimensional measurements
The functional field of dimensional measurements includes tactile or non-contact technologies, such as data acquisition using optical, capacitive or inductive measurement methods.
Force and torque measurements
We use piezoelectric sensors or strain gages to analyze the applied force or torque, measured in newtons (N) or newton-meters (NM).
Noise testing
During noise testing, the vibration behavior of a product is measured using a corresponding air-borne or structure-borne noise sensor, which behavior is then used to derive quality-relevant characteristics.
Fluid and component dynamics
Fluid and component dynamics is concerned with the movement of liquids or gases in systems or with the dynamics of the systems themselves. Methods in this field include testing pressure and tightness or speed, travel or the force-travel curve.
Surface testing
The surface quality evaluation involves technologies for recording waviness or roughness on components.
Electrical testing
Electrical testing is used to collect data on switching times, switching currents, voltage, insulation and resistance. These tests often relate to safety and are used to determine that the electrical components are functioning properly and do not present a danger to the environment.
Mechanical testing
Mechanical tests are an important part of material testing and are used to ensure the correct material properties. Hardness or penetration in the event of surface defects are measured, for example.
Non-destructive testing technology
Non-destructive testing technology (NDT) prevents the components under analysis from being damaged and destroyed. Some customary methods used for non-destructive testing are eddy current or ultrasonic tests.
Example applications for testing systems from Schaeffler Special Machinery
High-speed inline tests
Alongside complex testing systems for extensive test spectra, we are also able to meet high-speed measurement requirements. One example of this is our inline testing machine for cylindrical rollers. With a test output of 220 parts per minute, our compact machines are best in class for assuring quality in your production concept – from demagnetization to testing of all surfaces.
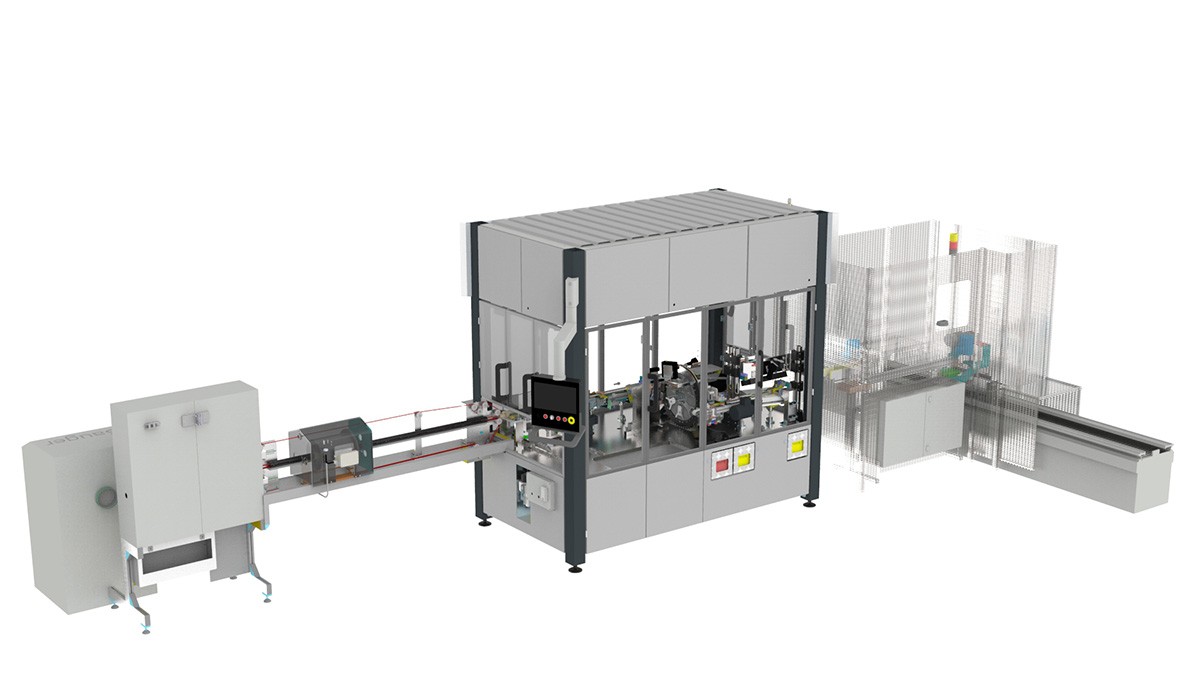
Grouping machines
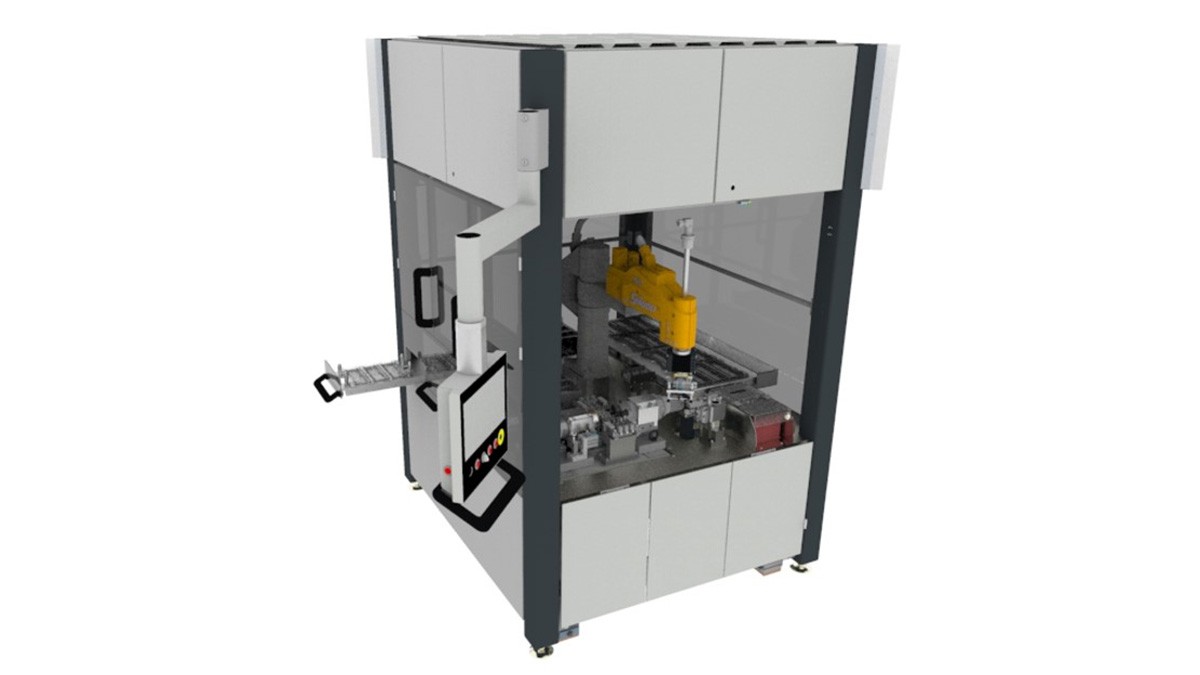
If components have requirements relative to each other that are based on specific criteria, sorting or grouping machines can be used. Grouping can be based on size, weight, shape or other criteria, for example.
The machine shown in the image sorts threaded shafts into three groups. The threads are rotated and the diameters recorded at three defined positions at a rate of 3.6 pieces/minute. The degree of accuracy achieved is 0,1 µm with a group width of 7 µm.