Additive manufacturing with metals in multi-material technology
Additive manufacturing processes are now widely used in both the private and industrial sectors. The application of material - pixel by pixel - leads to a completely new freedom of design, individualization and a reduction in manufacturing costs.
While additive manufacturing or metal 3D printing is already an impressive technology, the combination of different materials in an additive manufacturing process opens up completely new horizons. Our technology enables the seamless combination of different materials in a single manufacturing process - even in volume production. Additive manufacturing is more than just a trend - it is a paradigm shift in production.
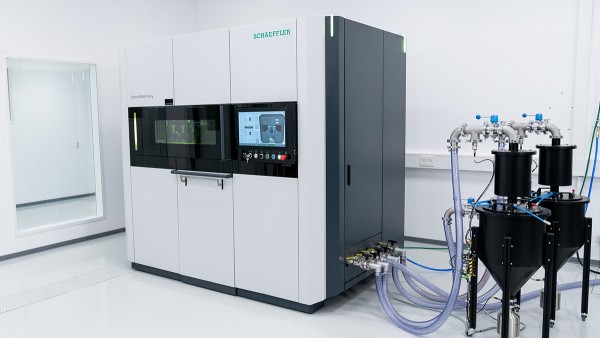
Together with Schaeffler Aerosint, our expert for selective material deposition, we have developed a unique system for additive manufacturing in an industrial environment. With our LPBF technology (Laser Powder Bed Fusion), components made of metal and technical ceramics can be produced in a composite - with up to three different materials simultaneously. In addition to 3D printing, we offer a holistic manufacturing approach from the design of the 3D geometry through printing and quality assurance to the finished component.
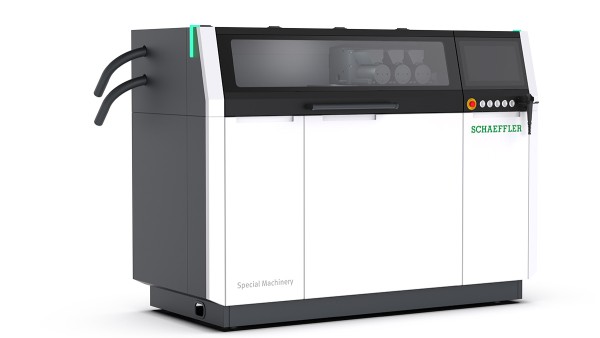
Our multi-material machine for high build rates and difficult-to-weld materials. With the unique Schaeffler Aerosint Recoater, up to three materials can be precisely and selectively built up in one mold. In contrast to OmniFusion 3D, which uses a laser-based process, the OmniForm 3D applies a pixel-precise process to build up the powder into a three-dimensional powder body, which is then heat-treated at high temperatures in a second, separate process step involving field-assisted sintering technology.
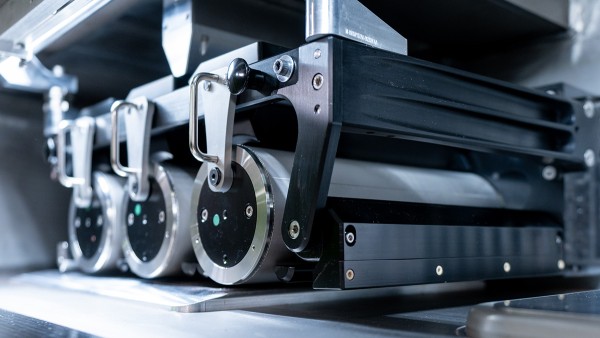
The Recoater is one of the key elements in 3D printing technology for multi-materials. Schaeffler Aerosint's innovative and patented recoater technology enables different materials to be applied to the powder bed quickly, precisely and flexibly in all spatial directions. This opens up a whole new level of possibilities and the opportunity to create unique designs, applications and customized material properties in industrial quality.
Application area for metallic multi-material components
Additive manufacturing with multi-materials is not only an exciting technical advance, but also a catalyst for completely new approaches in design and production. From our point of view, the following industries are particularly interesting for the use of our innovative systems:
- Aerospace: production of high-strength components with maximum rigidity and minimum operating weight
- Space & Defense: Components with maximum performance by combining the advantages of different materials
- Medical technology: Personalized implants and prostheses in combination with biocompatible materials for maximum patient comfort
- Automotive industry: Tool-free production of highly complex powertrain components such as electric motor components and heat exchangers
- Electronics: Integration of conductive materials and insulators in one component for compact and powerful devices
- Tooling: Combination of high-strength tool steels with materials with high thermal conductivity, e.g. injection molding inserts, for improved component quality and cycle time
- Prototype construction: Detailed and precise in high quality - for optimal support of the iteration process in prototype construction
Trusted partnerships in additive manufacturing - our references at a glance
In 2023, Schaeffler Special Machinery decided to enter the Additive Manufacturing market, followed by the acquisition of Aerosint, a specialist in multi-material powder recoaters. AMPOWER proved to be a valuable partner during our market entry, providing unbiased market intelligence and strategic guidance that supported our successful launch.
Have we piqued your interest? Please contact us for further information, individual advice on your application or if you are interested in a print.