AGV systems in (intra)logistics and assembly
The vision of autonomous production requires the value stream as a whole to be considered. Self-driven production control based on demand and condition data must also include concepts for an automated material flow. Modern industrial solutions thus require flexible concepts that push the use of automated guided vehicle (AGV) systems.
Automated guided vehicles (AGVs) are floor-bound conveyor systems that are automatically controlled and steered without contact. Intelligently connecting these vehicles to the master control system und the machine results in an automated guided vehicle system (AGV system). The areas of application are many and varied.
Three areas of application for AGV systems
Logistics
Commissioning and transport of materials and components between different storage locations (indoor and outdoor between storage and production buildings)
Intralogistics
Delivery or distribution of materials and components to different machines and systems from the central material supply point
Process module chaining
Material supply, as an alternative to rigid interlinking or as a flexible connection to individual process islands in the assembly and testing of products and product types
Boundary conditions and benefits for AGV systems
Various boundary conditions must be checked before AGV systems can be implemented. In particular, the question as to the strategy for using such systems should be clarified first.
Successful implementation of AGV systems for automating production is based on:
- a consideration of the upstream and downstream material flow
- a review of IT conditions
- an evaluation of safety and the location of use
- selection of the right manufacturer or vehicles.
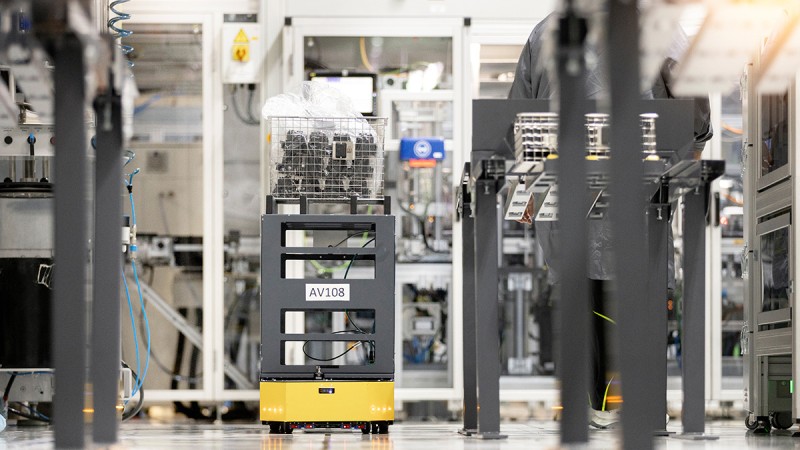
In consideration of these aspects, economical logistics solutions can be implemented between production steps or even within the production concept itself. If the AGV systems can communicate with the machines, this ensures that relevant interfaces, e.g. for acquiring workpiece carriers, are secured.
Our experts identify the best systems for you in consideration of the supply of material and whether it can be reused in upstream and downstream processes. Well-planned AGV system concepts reduce production costs for linked employees in non-value-creating activities. Compared to rigidly chained systems, they offer the benefit of higher flexibility. These mobile solutions also often require significantly less space during implementation.
AGV systems in the assembly and testing line for e-axle systems
Our assembly line for electric axle drive systems uses three AGV systems for transporting materials between the two pre-assembly lines and the final assembly line. At specially designed transfer stations, the pre-assembly assemblies are transferred to the AGV systems and, from there, to the final assembly line and testing line. On the way back, the empty workpiece carriers are transferred back to the pre-assembly lines.
The AGV systems communicate directly with the production machines via the communication interface according to the VDA5050 standard and drive autonomously to the charging stations during breaks or downtimes. By ensuring an optimized arrangement of the individual lines and a separation between logistics side and operator side, employees and AGV systems can work alongside one another with no major overlaps or path crossings.
Mobile robots
For tasks that are repeated often or if the production concept is arranged into process islands, location-independent automation solutions can be combined by connecting AGVs and cobots. These are known as mobile robots and can automatically drive to any desired station. This means that transport and value-creating processes can be viewed with a common solution. This type of production is not suitable for mass production of series parts; however, when it comes to automating small quantities or covering a wide variety of types with corresponding production islands, the implementation of mobile robots can free up manual capacities and increase efficiency.
As sensor technology and AGV capabilities continue to evolve, this modularity of the robotic systems can help to improve reusability across projects in the future, thus reducing capital investment.
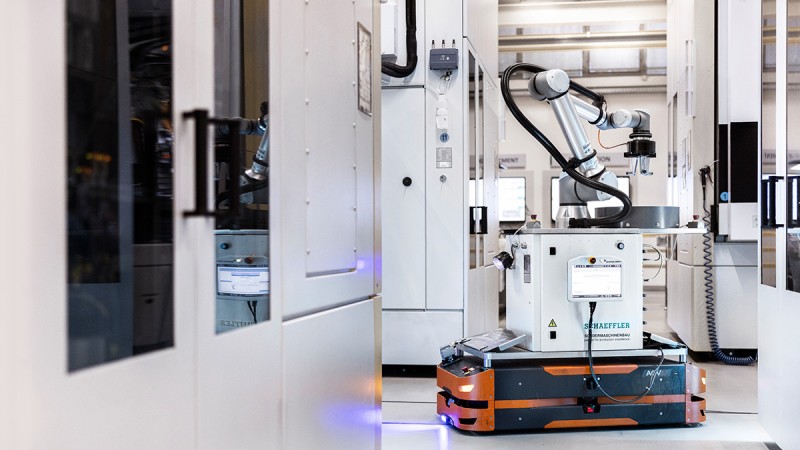