Milestone in additive manufacturing | Multi-material 3D printing with our OmniFusion 3D
In many areas, additive manufacturing has already established itself as an alternative to the conventional production of workpieces. Multi-material 3D printing opens up almost unlimited possibilities and represents a genuine revolution in the manufacturing industry.
Together with Schaeffler Aerosint, we have developed a system for additive manufacturing that can produce 3D printed parts using a combination of metals and technical ceramics. The OmniFusion 3D enables:
- Unparalleled design freedom
- Unique material combinations
- Integration of several material properties in a single component
- Individualization and needs-based production
Our system, specially developed for 3D multi-material printing, sets new standards in additive manufacturing with multi-materials and represents a milestone in the application of additive manufacturing processes.
Our multi-material printing process
With our patented technology, individual layers of the component geometry are applied to the print bed with pixel precision and fused layer by layer to form the finished part. Materials are fed to the Recoater from integrated powder reservoirs or an external powder supply, and the various powders are arranged as needed on the build platform and deposited. During the scanning process, the components are built up layer by layer using a laser. Up to 4 laser beam sources can be used to efficiently process a variety of metals or technical ceramics. The printing process itself takes place in a closed process chamber that is flooded with argon shielding gas. Our innovative technology enables the use of up to three different materials.
You can find out more about our patented recoater technology and the individual placement of the material on the powder bed hier.
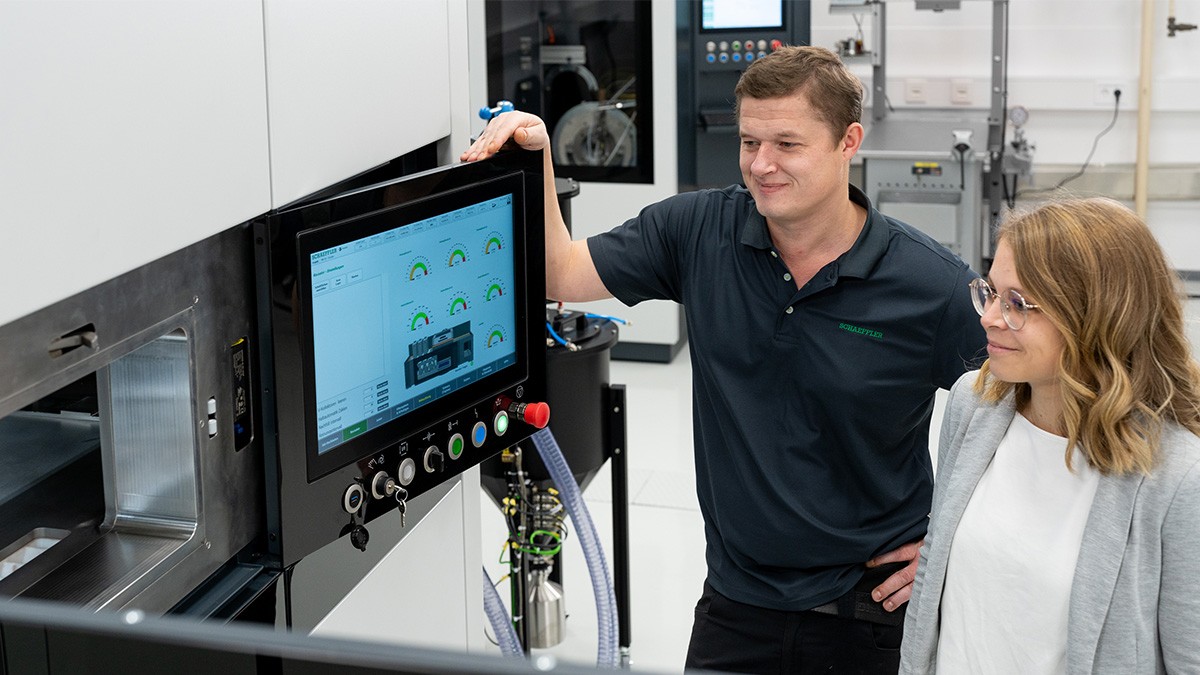
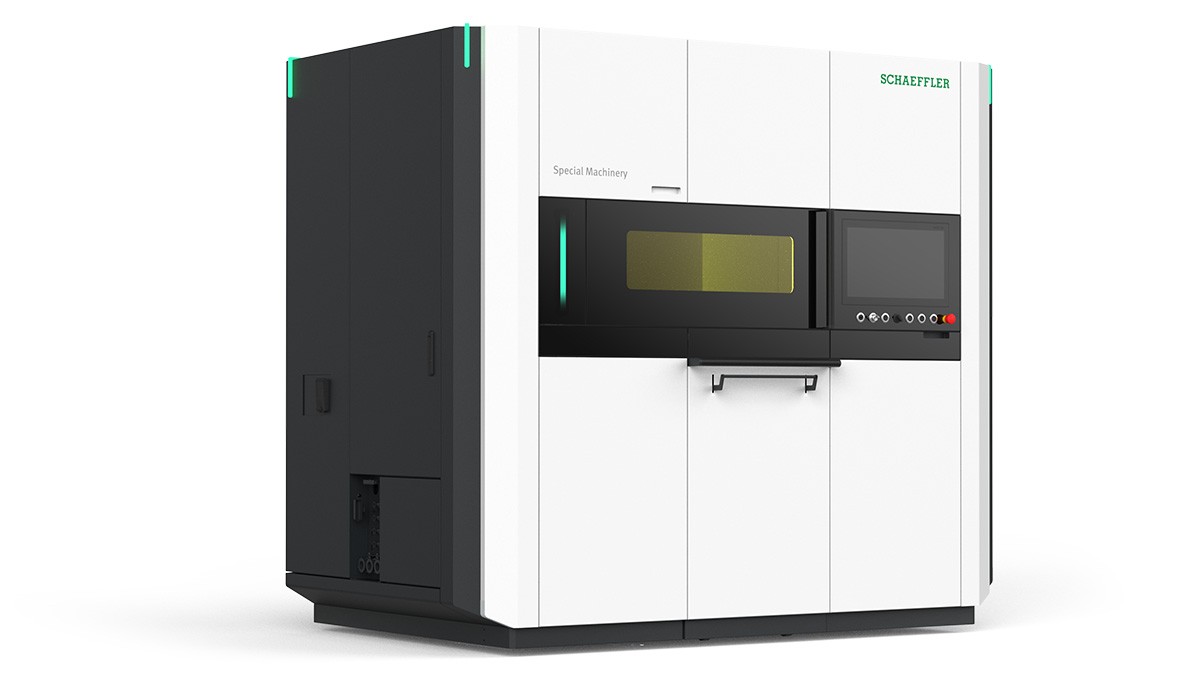
System details of our OmniFusion 3D
- System size: 2525 x 1696 x 2271 mm
- Component size: approx. 250 x 250 x 250 mm
- Pixel size: 300 µm
- Layer thickness: 40-200 µm
- Density: up to 99.8 % for various materials
- Print speed: 10 - 100 cm³ / hour
- Spot size: 50-300 µm
Holistic production approach for additive manufacturing in mechanical engineering
We pursue a holistic production approach from the design of the 3D geometry to the finished component. Together with our partners, we offer a range of services that includes the printer and operating software as well as the provision of printing material. Supplementary services such as "design to print" or the measurement and testing of workpieces ensure the robust production of 3D-printed products.
Our unique expertise in 3D multi-material printing lies particularly in our know-how for the right materials and advice on individual product design. Our knowledge of the optimum machine parameters contributes to excellent printing results.
Customer benefits through multi-material printing
Additive manufacturing has long since established itself in many areas as an alternative and supplement to the conventional production of workpieces, after centuries of sawing, grinding, milling or ablation. Multi-material 3D printing opens up completely new possibilities here.
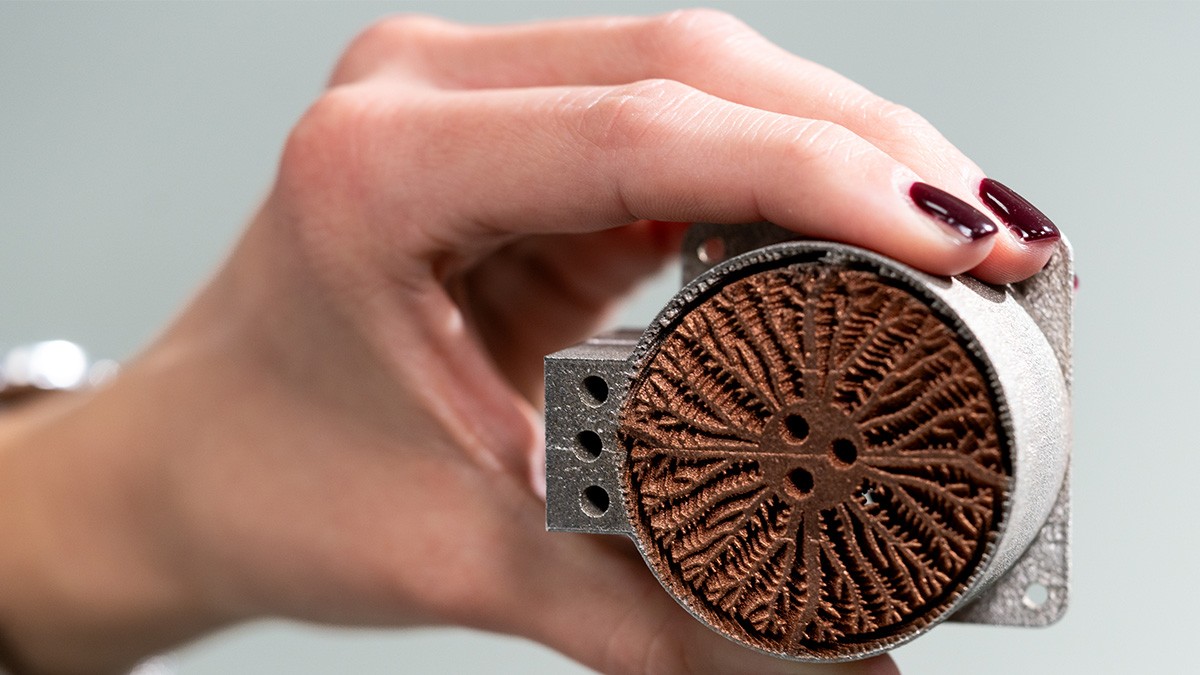
Advantages of multi-material production
Extended design freedom and functional integration: Additive manufacturing in general enables product designers to realize free geometries that are not possible with traditional manufacturing methods. Additive manufacturing in combination with different materials offers additional flexibility to meet individual performance requirements through specific material properties. By combining different material characteristics (e.g. hardness, electrical conductivity, strength, thermal conductivity, corrosion resistance) in one component, products with integrated multifunctionality are created that were previously only technically feasible through complex joining processes or not at all.
Optimized use of materials:By using different materials exactly where they are needed, multi-material production reduces material waste and significantly improves resource efficiency.
Shorter production times: Additive manufacturing eliminates the need for many traditional manufacturing processes, such as casting or forging, dramatically reducing production time and time to market.
Are you interested in our OmniFusion 3D? Please feel free to contact us. In a personal meeting, we can give you a deeper insight into additive manufacturing and our OmniFusion 3D and advise you individually on your application.