Virtuelle Inbetriebnahme als Beitrag zur Digitalisierung
Die zunehmende Digitalisierung der Produktion bringt für Unternehmen einige entscheidende Vorteile. Digitale Zwillinge der realen Anlagen können die Effizienz und Qualität der Fertigung erhöhen oder Kosten reduzieren. Die Betrachtung von Maschinen als Simulation in virtuellen Umgebungen kann Möglichkeiten eröffnen, die ohne digitale Abbilder nur mit hohem Aufwand oder Stillständen verbunden wären.
Vorteile durch virtuelle Inbetriebnahmen
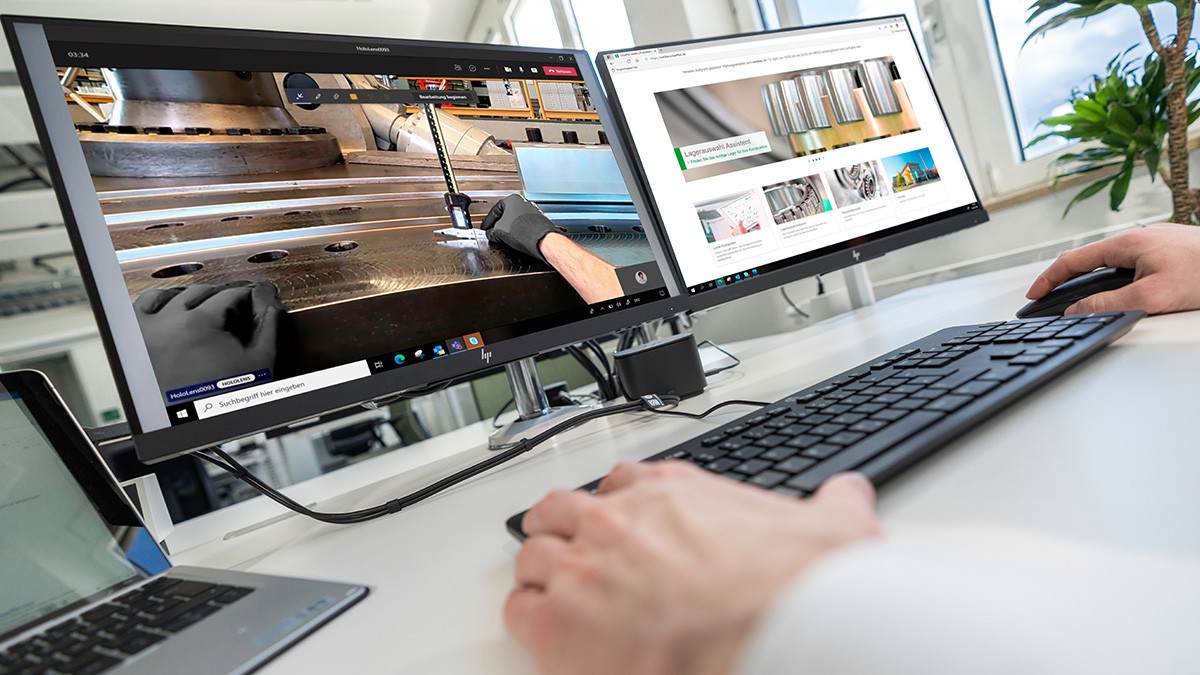
Die Simulation von Prozessen und Funktionen ist zunehmend eine zentrale Komponente in der Entwicklung von Produktionskonzepten. Die Arbeit in verschiedenster Software mit virtuellen Modellen beginnt bei Schaeffler Special Machinery ab der Erstellung des Konzeptes und begleitet die Maschinenentstehung von den ersten Schritten bis zur Serienproduktion bei unseren Kunden vor Ort.
Virtuelle Inbetriebnahmen helfen uns eine kosteneffiziente, nachhaltige Fertigung zu gestalten und dem globalen Wettbewerb standzuhalten. Durch virtuelle Inbetriebnahmen können wir die Time-to-Market und die Stabilität unserer Anlagen verbessern. Im laufenden Betrieb der Anlagen können digitale Zwillinge weiterhin zur Steuerung, Optimierung und Flexibilität der Produktion beitragen.
Test in der Simulation
In der Vergangenheit war die Realisierung von Maschinen ein sequenzieller Prozess. Die Programmierung der Steuerung (SPS-Programmierung) und integrierten Roboter usw. konnte mit bzw. nach der Montage der Anlagen in unserer Werkstatt gestartet werden. Die Parallelisierung der Softwareprogrammierung zur Montage neuer Maschinen führt zur:
- Verkürzung der Realisierungszeit
- Erreichung robusterer Prozesse zu früherem Montagezeitpunkt
- Validierung und Test der Software, Schnittstellen und Prozesse durch digitale Abbildung
- Reduktion der Risiken im Projekt und Verkürzung der Lieferzeiten
- Minimierung der Wartezeiten in realer Inbetriebnahme
- Größere Agilität durch Anpassungen an unseren Systemen über den digitalen Zwilling
Durch die virtuelle Inbetriebnahme wird die Flexibilität auch bei Neukonfigurationen oder Nachrüstungen erhöht. Die Effizienz in Zeit und Ressourcen kann dadurch erhöht werden.
Schulungen und Trainings
Ein großer Vorteil der virtuellen Inbetriebnahme mit einem digitalen Zwilling ist die Möglichkeit, Schulungen und Trainings für Mitarbeitende unserer Kunden, an diesen Modellen durchzuführen. Zusätzliche Technologien, z. B. Virtual oder Augmented Reality, können auf Basis des digitalen Systems die realen Maschinen erlebbar machen. Schulungen können, am laufenden Modell und von überall auf der Welt, durchgeführt werden. Funktionen, mögliche Fehlerbehebungen oder regelmäßige Kalibrierungs- oder Wartungsaktivitäten werden an den digitalen Zwillingen unserer Systeme gezeigt und erlernt. Die Qualifizierung der Mitarbeitenden ist somit kostengünstiger, intensiver und zeitlich unabhängiger.
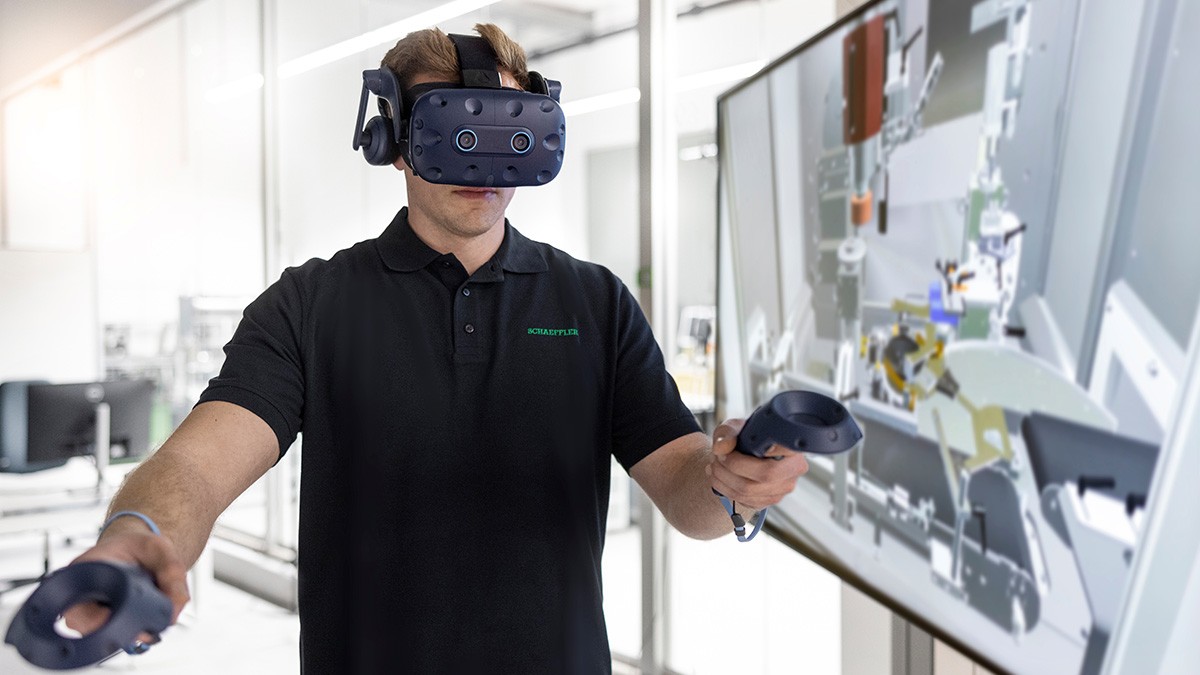
Beispiel eines digitalen Maschinenzwilling im Rahmen einer virtuellen Inbetriebnahme
Das Video zeigt die digitale Simulation von Bewegungen und Prozessabläufen an einer kleinen Stand-Alone-Maschine. Zeitgleich zur Montage der realen Maschine wurden alle Softwarebausteine, die im Programm verwendet werden, in einer virtuellen Simulation getestet und optimiert. Der optimale Prozessablauf und die kürzeste Taktzeit konnten somit bereits vor der Inbetriebnahme der Maschinenfunktionen realisiert werden.
Die Idee einer vernetzten Produktion
Eine vernetzte Produktion und digitale Zwillinge stehen in enger Beziehung zueinander und bilden zusammen ein wichtiges Konzept im Bereich der Industrie 4.0. Das Maschinenmodell ist eine digitale Kopie des physischen Systems die kontinuierlich in Echtzeit mit Daten gespeist wird. Der Zwilling kann auf dieser Basis dazu verwendet werden, Vorhersagen über zukünftige Ereignisse und Probleme zu treffen, um diese proaktiv zu lösen bevor sie in der realen Welt auftreten. Durch den Einsatz von Algorithmen und KI-Technologien können diese Datenauswertungen und Maßnahmenableitungen automatisiert unterstützt oder autonom getroffen werden.
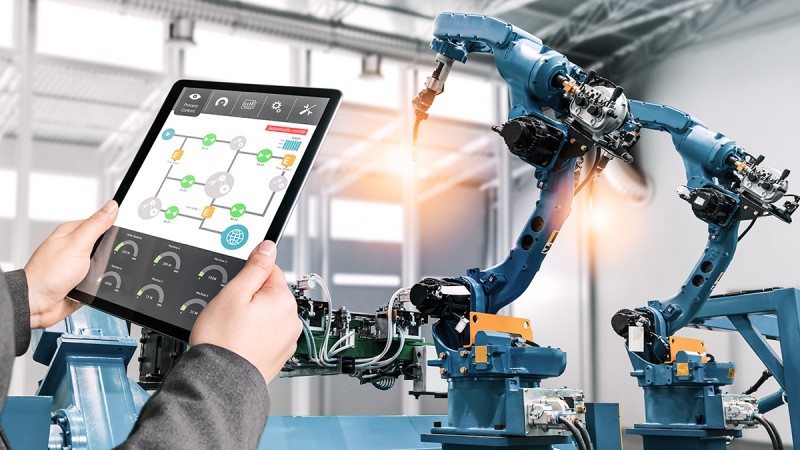
Case sudy: Mehr PS durch virtuelle Inbetriebnahme
Da die Komplexität der Automatisierung und Digitalisierung zunimmt, verbessern wir unsere Engineering-Prozesse durch virtuelle Inbetriebnahmen. Die Partnerschaft mit der F.EE Group und deren fortschrittliches Simulationstool fe.screen-sim ermöglicht es, Steuerungsstrategien bereits in einer frühen Projektphase zu testen und zu optimieren. Die Software bietet simultanes Engineering, so dass die Teams an der Entwicklung arbeiten können, während sich das Produktdesign weiterentwickelt. Virtuelle Inbetriebnahmen reduzieren den Zeitdruck erheblich und erhöhen die Systemqualität, während gleichzeitig die Zusammenarbeit zwischen verschiedenen Teams auf der ganzen Welt gefördert wird. Durch die weltweite Ausweitung unserer Simulationsdienste ist die Zukunft einer effizienten und rationellen Inbetriebnahme vielversprechend.