Beratung und Planung zur optimalen Produktionslösung
Eine optimale Produktionslösung ist wirtschaftlich effektiv, in bestehende Produktionsabläufe perfekt integriert, robust, flexibel, uvm. Um eine solche Lösung entwickeln und realisieren zu können, stehen Ihnen unsere Experten und Expertinnen als Partner für Produktionsexzellenz zur Seite. Durch einen engen Austausch in den frühen Projektphasen bzw. der Einbindung in das Produktdesign helfen wir Ihnen, die richtigen Weichen für zukunftsfähige und wirtschaftliche Produktionssysteme zu stellen.
Unsere Methodik zur Planung & Projektierung von optimalen Produktionslösungen
Design for manufacturing
Unter Design for manufacturing (auch Design for assembly) verstehen wir die Betrachtung von Montageabläufen bereits während der Produktentwicklung. Der Abgleich von Produktmerkmalen wie Materialien, Toleranzen oder die Festlegung von Prüfschritten mit den späteren Produktionsprozessen und -technologien ist der zentrale Bestandteil des Design for manufacturing. So kann bereits während der Produktentstehung durch eine ganzheitliche Betrachtung der Herstellkosten die Wirtschaftlichkeit des Produktes maßgeblich optimiert werden.
Unsere Experten und Expertinnen sind die Schnittstelle zwischen Produktentwicklung und Maschinenbau. Sie verfügen über langjährige Erfahrungen und beraten Sie gern. Der Blickwinkel des Design for manufacturing kann frühzeitig Produktionsprobleme und Produktionsfehler vermeiden. Die Qualität der Produkte kann verbessert und die günstigste Kombination aus Anlageninvestition und Kosten der Produktkomponenten gefunden werden.
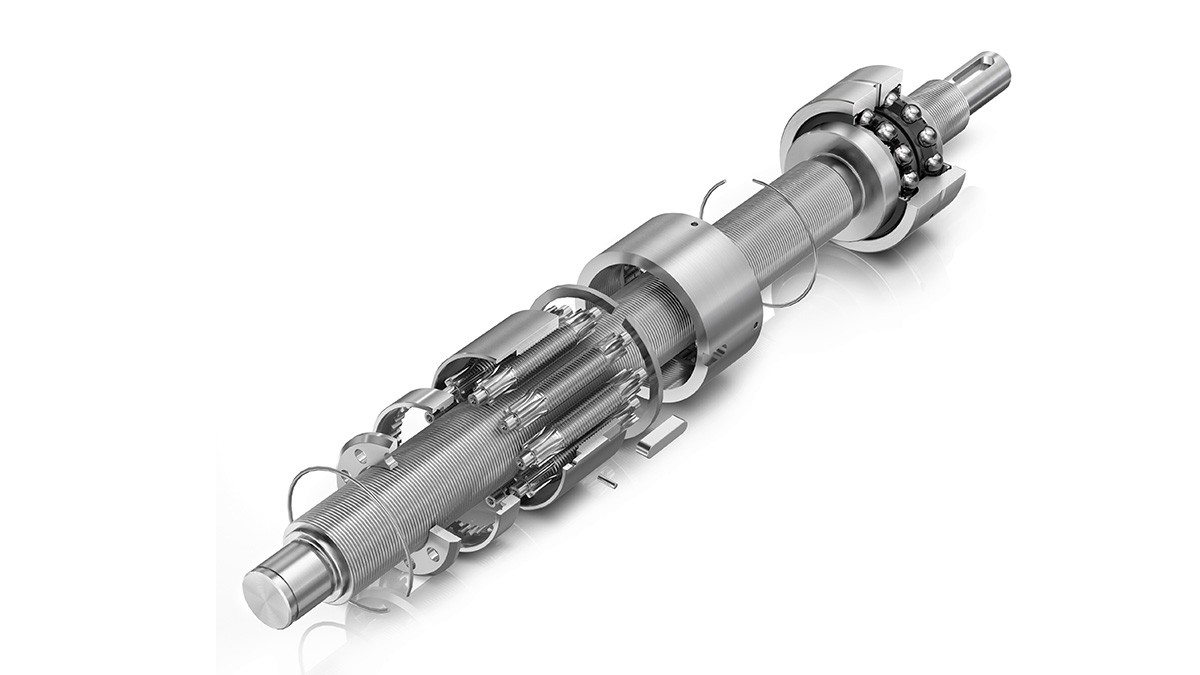
Projektierung
In drei Schritten zu individuellen Maschinen und Anlagen
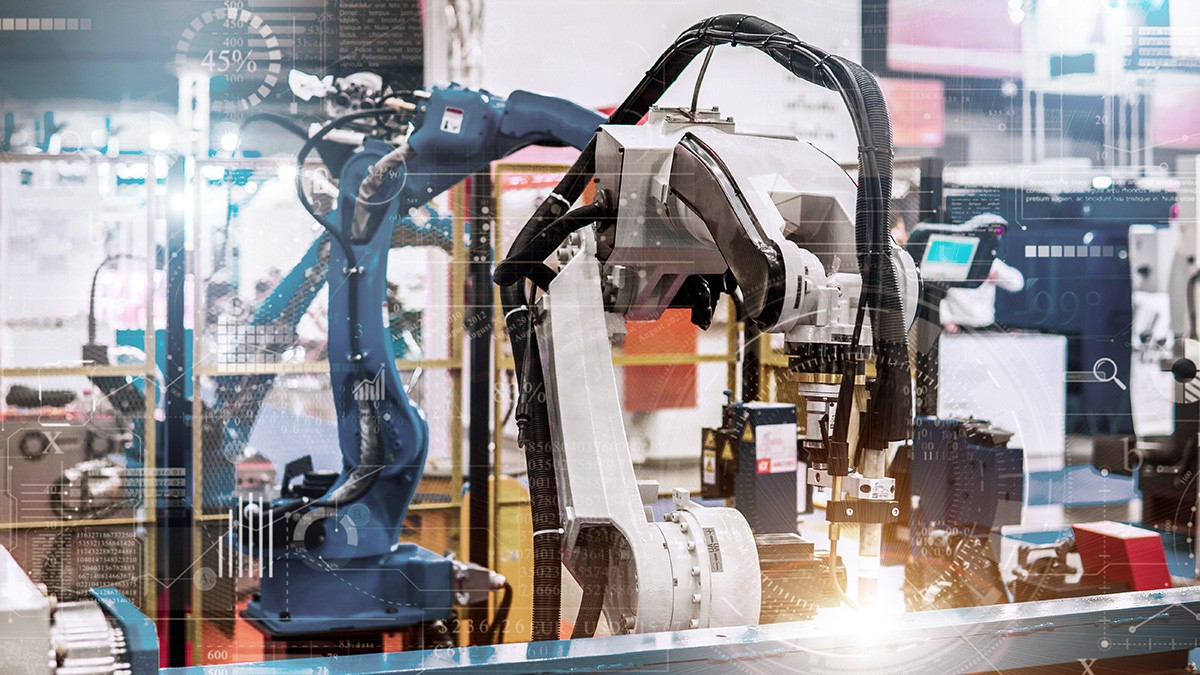
Definition von Arbeitsfolgen, Qualitätsanforderungen und Prozessen
Eine Arbeitsfolge ist, abhängig vom Produktaufbau, die räumliche und zeitliche Abfolge von technisch zusammengehörenden Arbeitsvorgängen an einem Arbeitsplatz. Die Definition der Arbeitsfolgen ist Grundlage für:
- Visualisierung der Montagefolgen
- Ermittlung der Prozess- und Handlingsstufen
- Abtaktung von automatischen Prozessen und manuellen Tätigkeiten
- Planung der konstruktiven Ausgestaltung der Prozessstationen
- Vermeidung von Fehlerfortpflanzung in Folgeprozesse
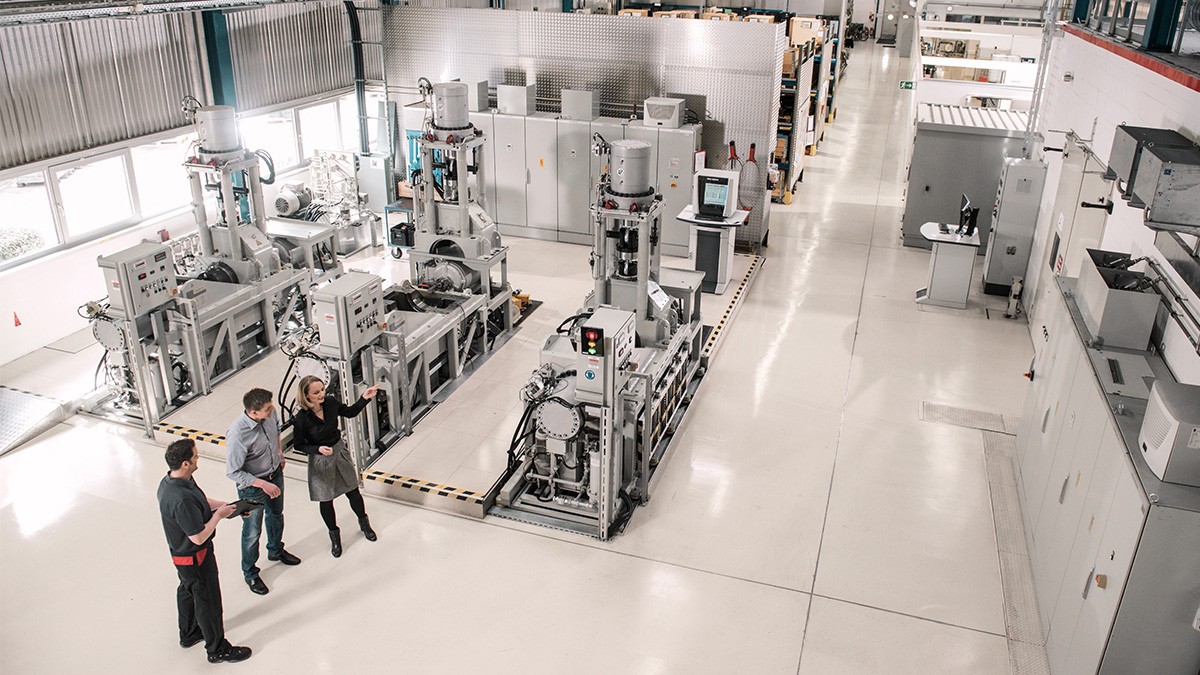
Ermittlung der Abtaktung
Aus dem Verhältnis der verfügbaren Netto-Produktionszeit/Zeiteinheit zur geforderten Stückzahl/Zeiteinheit ergibt sich Ihr Kundentakt. Ihr individueller Fertigungstakt wird auf Basis Ihrer Produktionsplanung und dem Kundentakt errechnet. Dabei werden z. B. die Anzahl der Schichten, der Nutzungsgrad oder kurzzeitig erhöhte Ausbringungsmengen berücksichtigt.
Mit diesem Fertigungstakt werden sowohl automatische Prozesszeiten als auch manuelle Tätigkeiten abgeglichen, um eine gleichmäßige und optimale Auslastung von Personal und Anlage zu erreichen. Für stark schwankende Bedarfe bieten wir spezielle, kapazitätsflexible Anlagengestaltungen an.
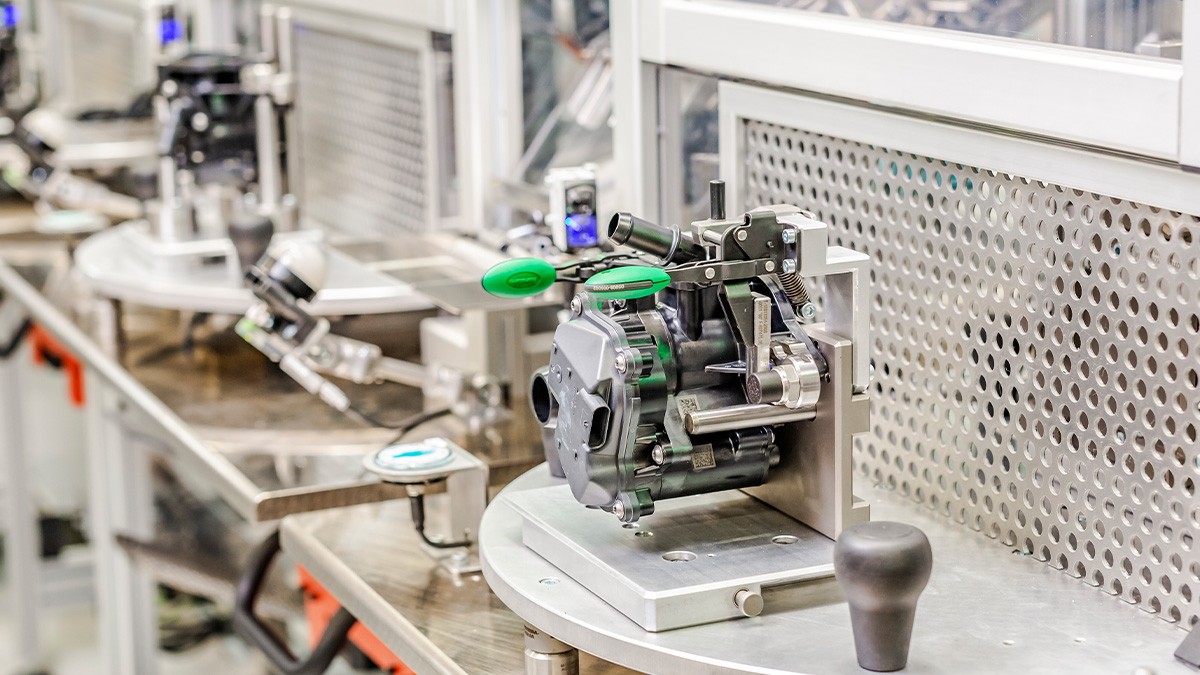
Auswahl des geeigneten Maschinenkonzepts & Bewertung der Wirtschaftlichkeit
Bei der Auswahl des geeignetsten Maschinenkonzepts reicht unser Angebot von manuellen, ergonomisch optimierten Arbeitsplätzen über vollautomatisierte Serienanlagen, bis hin zu kurvengesteuerten Schnelltaktern. Im Fokus unserer Layoutentwicklung steht immer die Wirtschaftlichkeit im Sinne des Investitionsvolumens sowie der Total Cost of Ownership (TCO).
Folgende Faktoren haben Einfluss auf unseren Konzeptvorschlag:
- Investitionen (CAPEX)
- Variantenvielfalt
- Taktzeit
- Notwendige Flexibilität für Bedarfsanpassungen
- Zugänglichkeit & Wartung
- Materialzuführung